Insert Injection Molding
Moreover, Insert Molding combines metal and plastics, or multiple combinations of materials and components into a single unit. The process makes use of engineering plastics for improved wear resistance, tensile strength and weight reduction as well as using metallic materials for strength and conductivity.
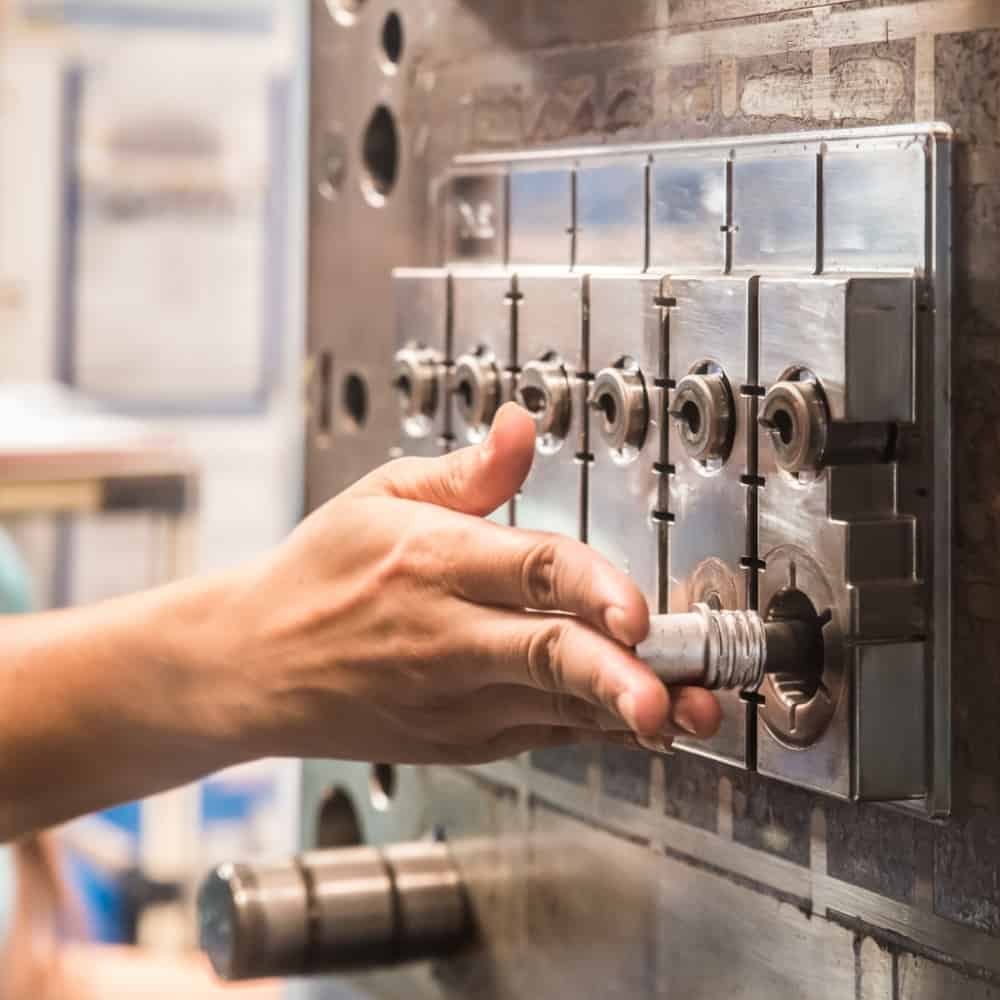
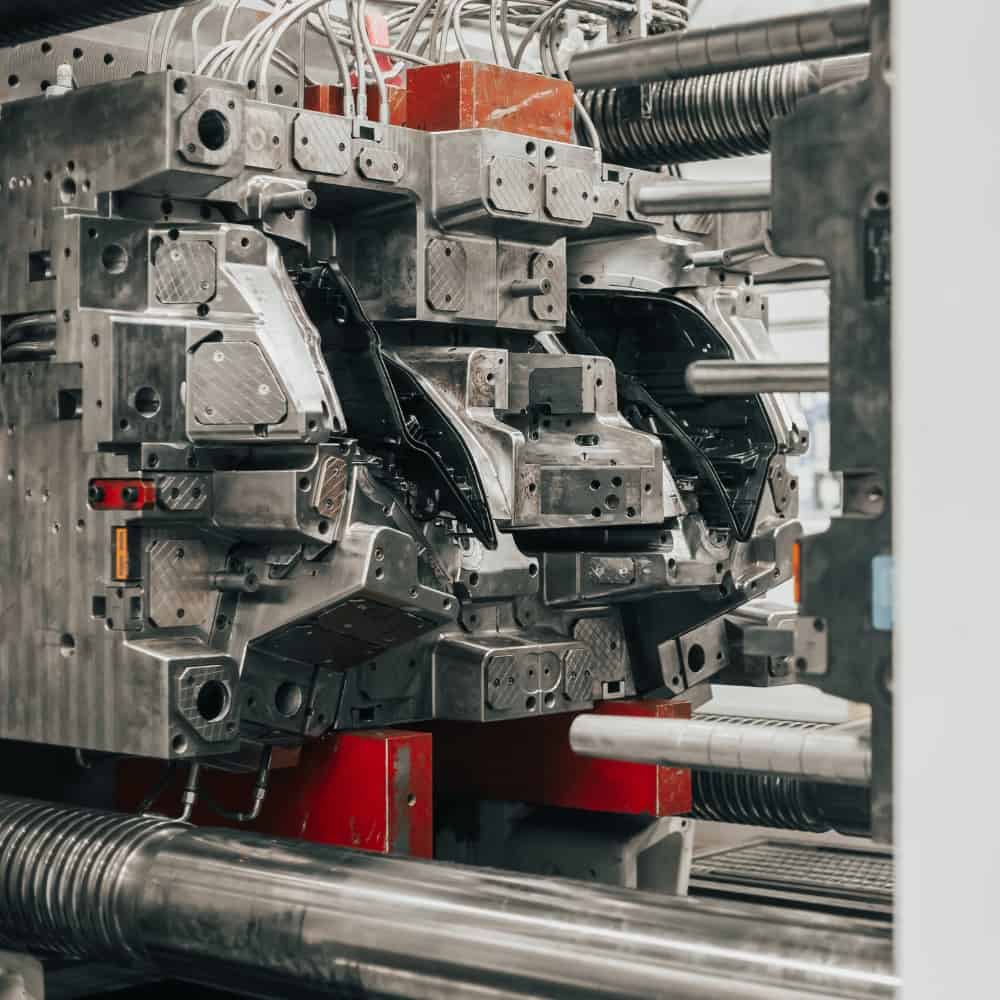
Insert Molding Process
Insert Injection Molding Benefits
Improves component
reliability
Improved strength &
structure
Reduces assembly &
labor costs
Reduces the size &
weight of the part
Enhanced design
flexibility
Insert Injection Materials
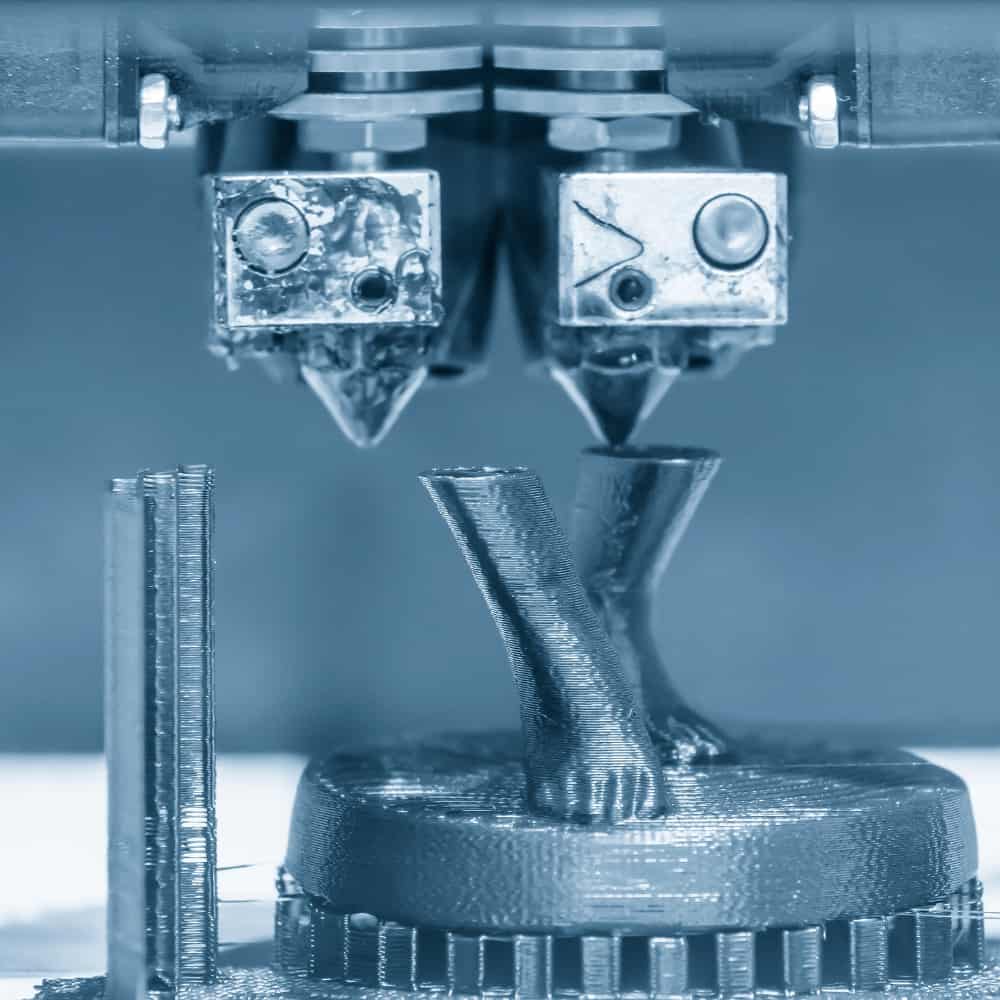
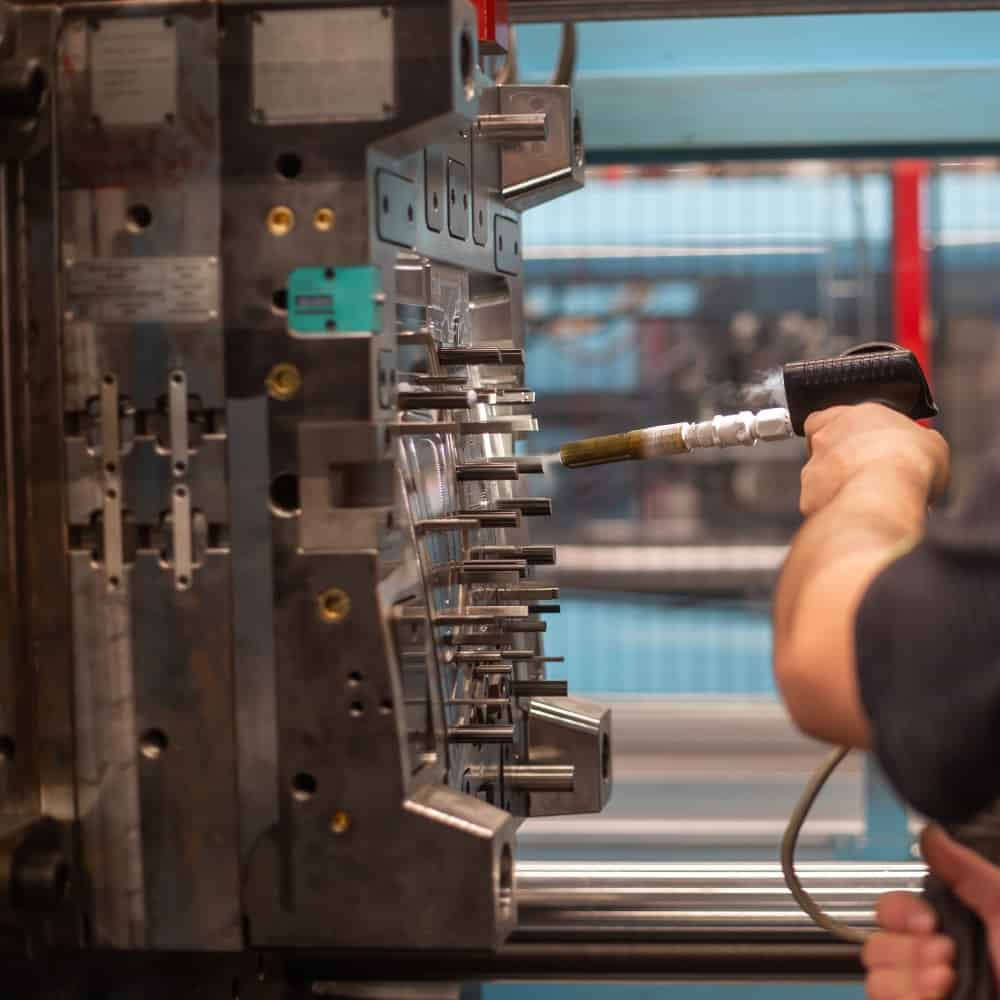
Applications & Uses for Plastic Injection Inserts
Insert molding metal inserts are derived directly from insert injection materials and are regularly used in a wide range of industries including: aerospace, medical, defense, electronics, industrial and consumer markets. The applications for metal inserts for plastic parts, include:
- Screws
- Studs
- Contacts
- Clips
- Spring contacts
- Pins
- Surface mount pads
- And more
Insert Injection Molding vs Overmolding
Insert molding and overmolding are two distinctly different processes that produce their own unique types of products. The overmolding process takes place when one material is overmolded over a second material. The base layer is molded first and the additional plastic layer(s) are molded over and around the original part. This results in a single finished product. Overmolding creates a strong finished product with long service life and enhanced safety features.
Conversely, insert injection molding occurs when insert injection materials are injected into the mold cavity prior to plastic injection molding. The resulting product is a single piece with the insert encapsulated by the plastic. Plastic injection inserts provide a fast and cost-effective assembly process, producing parts with reduced size and weight.
Insert Molding Considerations
- Means to hold the insert during the molding process
- Bosses or undercuts that provide additional retention strength within the molded part
- Understanding which specific components and technologies are combined into a single component within the insert injection molding process
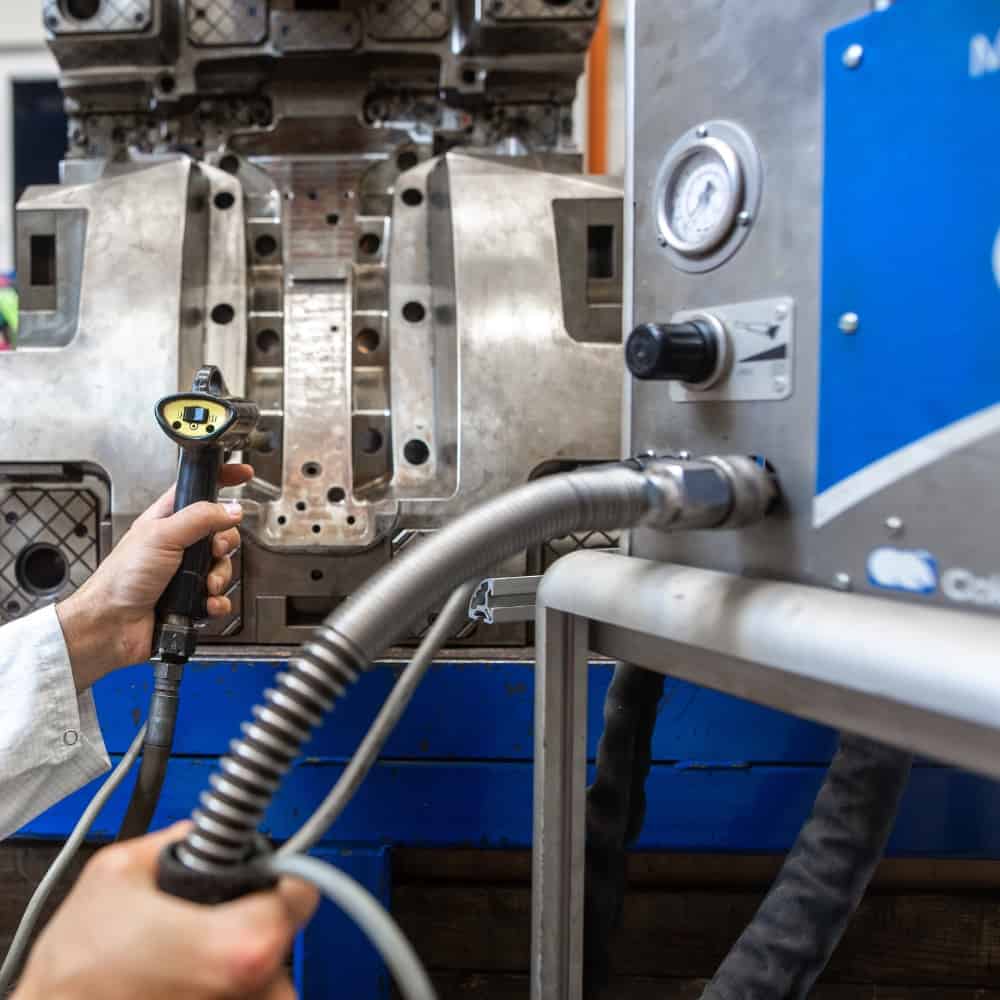
Where Material Meets Mastery
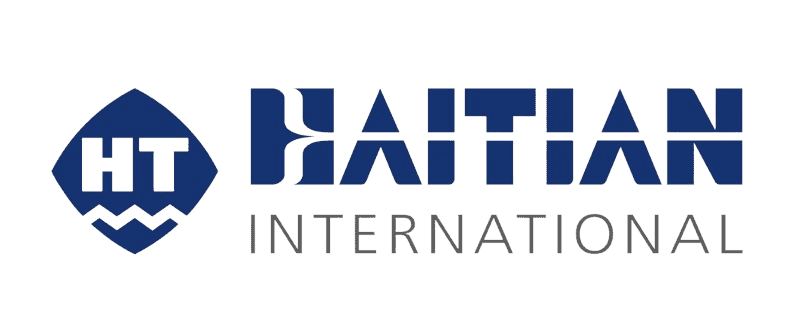
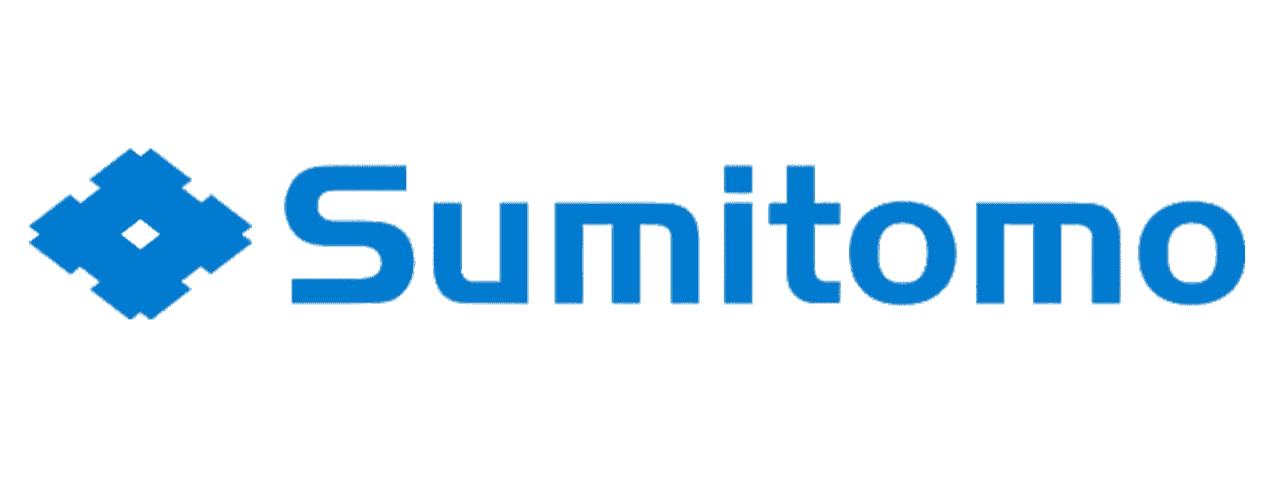
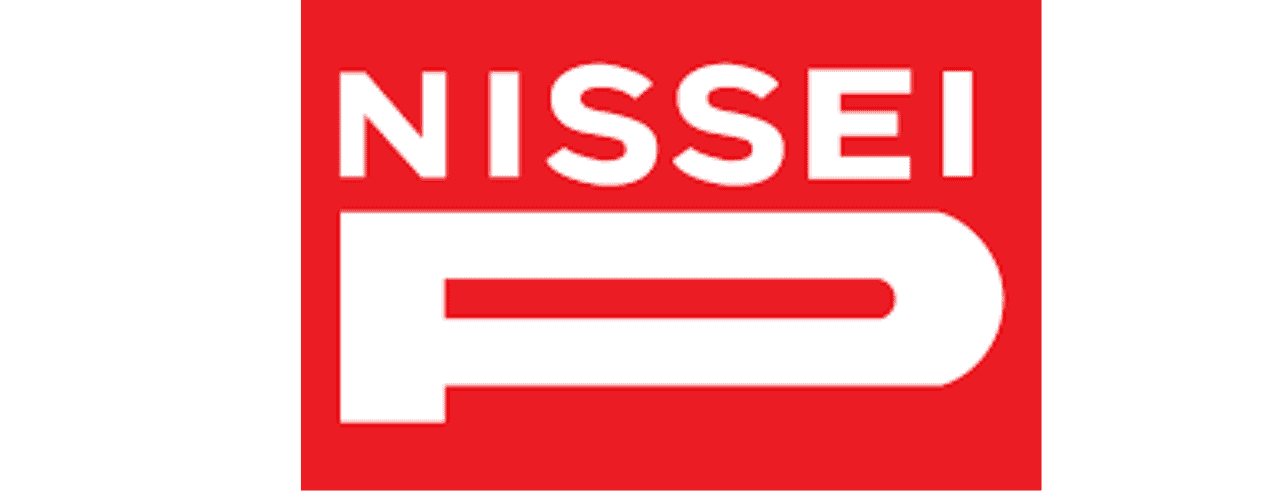
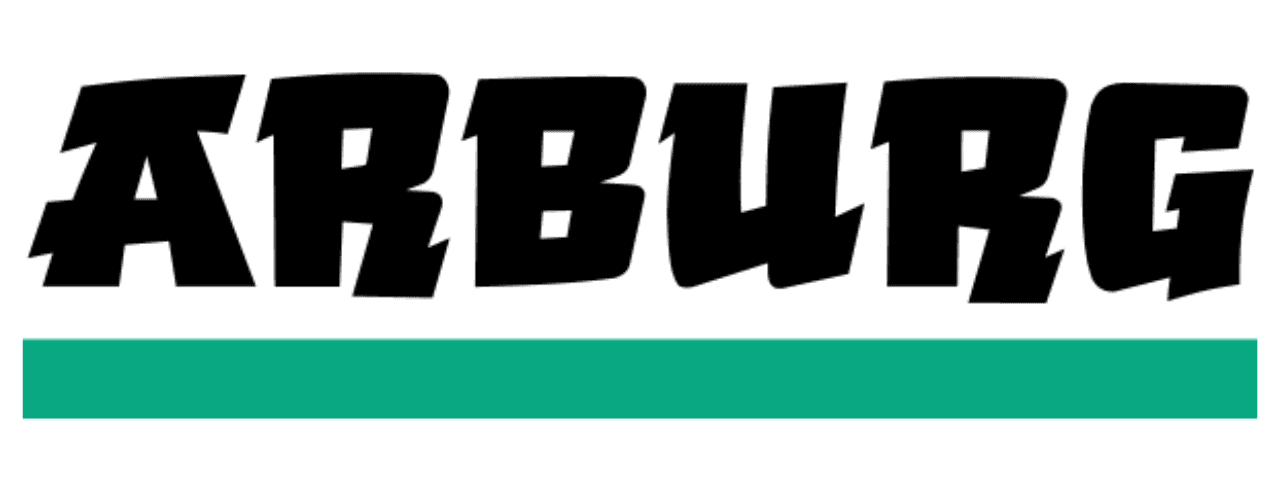