Mold Design
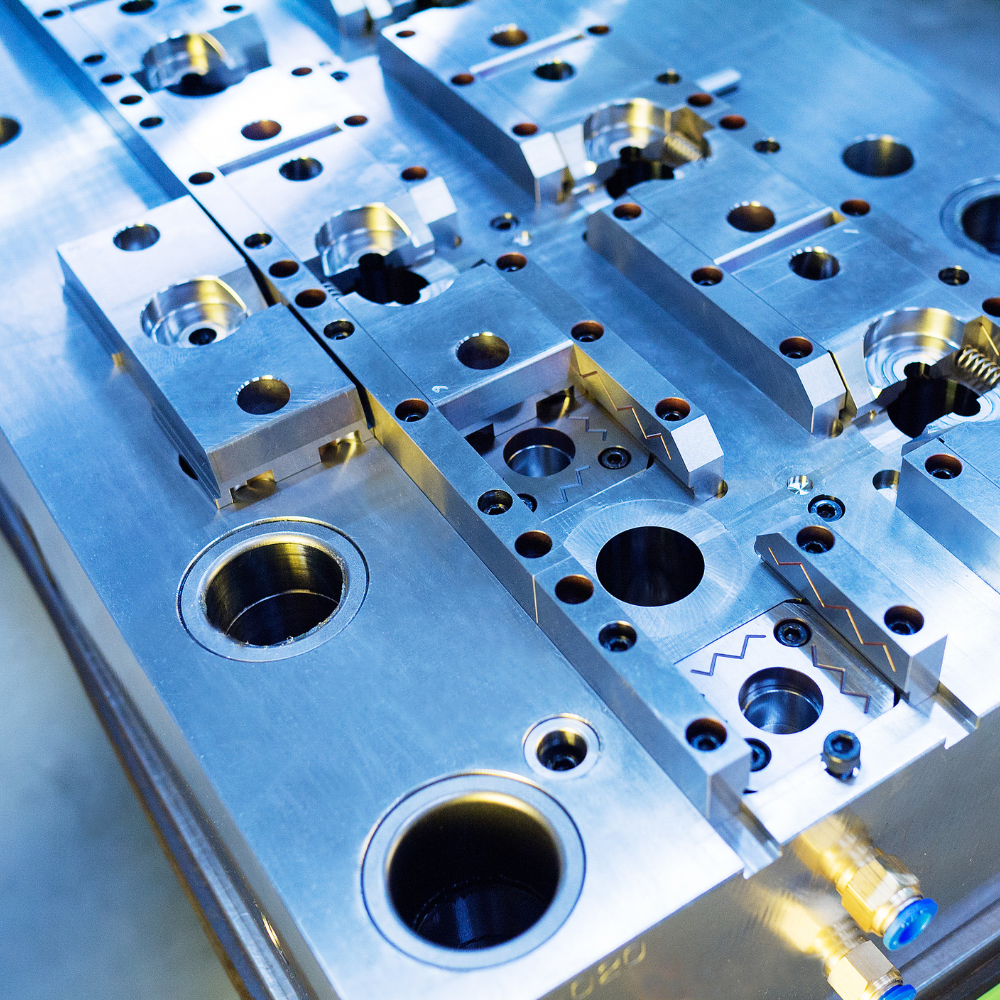
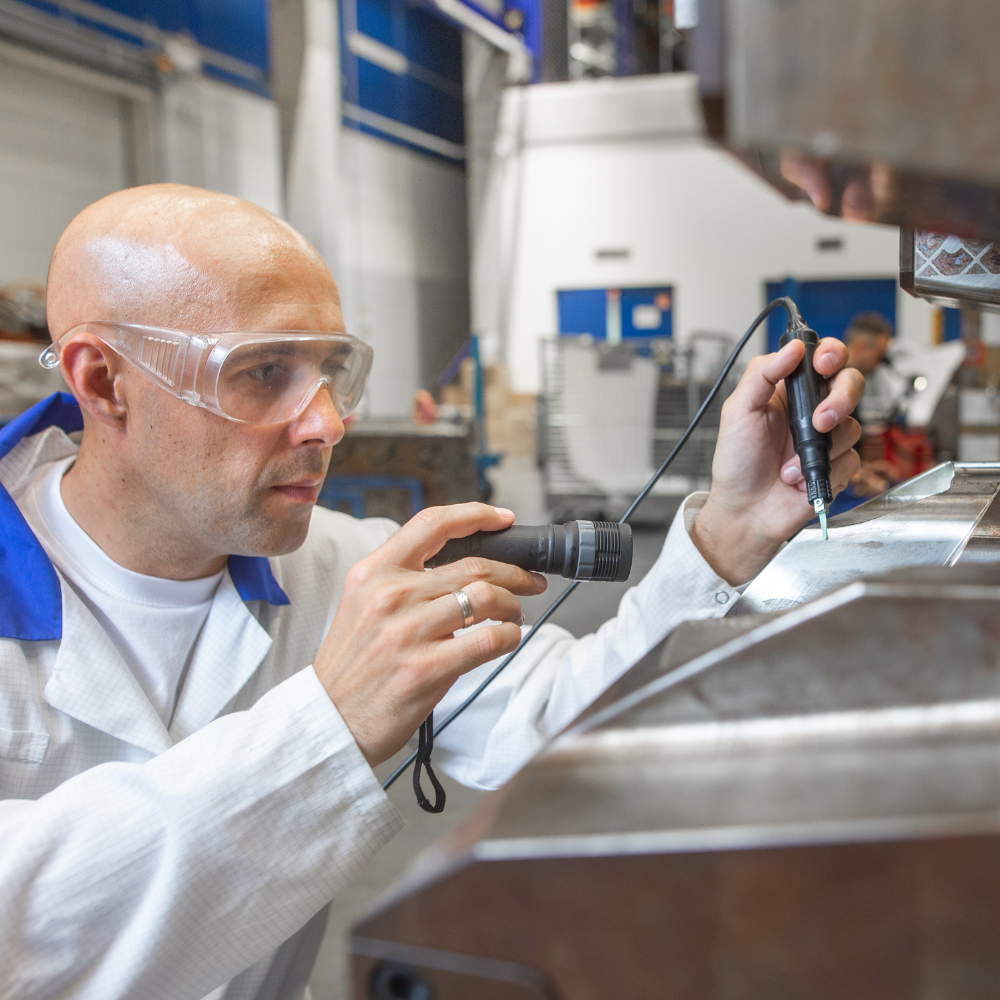
Production Mold Making Services
- Molds For Production Runs
- Ensuring part Consistency With Scientific Methods
- Comprehensive Analysis of Molds
- Proprietary automated CMM process With Relevant Reports
Why Choose Sonfuat for Mold Design?
Wide Range Of Molds
Quick Turnaround
DFM Reports
High Quality Molds
Process For Making Mold
Manufacturability Analysis
Our process begins with a thorough manufacturability analysis. This crucial first step involves assessing your design for feasibility and efficiency, ensuring the final mold will meet your specific requirements with optimal production efficiency.
Design & Flow Analysis
In this phase, our expert team undertakes detailed design and flow analysis. We utilize advanced software to simulate and analyze the mold design, ensuring perfect precision and quality in the mold flow, and identifying any potential issues early in the process.
Mold Making
With the design set, we move to the actual mold making. Our state-of-the-art manufacturing facilities and skilled craftsmen work together to fabricate the mold, adhering to the highest standards of accuracy and quality to produce a tool that precisely matches the approved design.
Sampling
Once the mold is created, we conduct a series of sampling runs. This critical step tests the mold in real-world conditions, ensuring it produces parts that meet all specifications and quality standards. Any necessary refinements are made during this stage to guarantee perfect output.
Shipping
Our process begins with a thorough manufacturability analysis. This crucial first step involves assessing your design for feasibility and efficiency, ensuring the final mold will meet your specific requirements with optimal production efficiency.
Available Production Molding Techniques
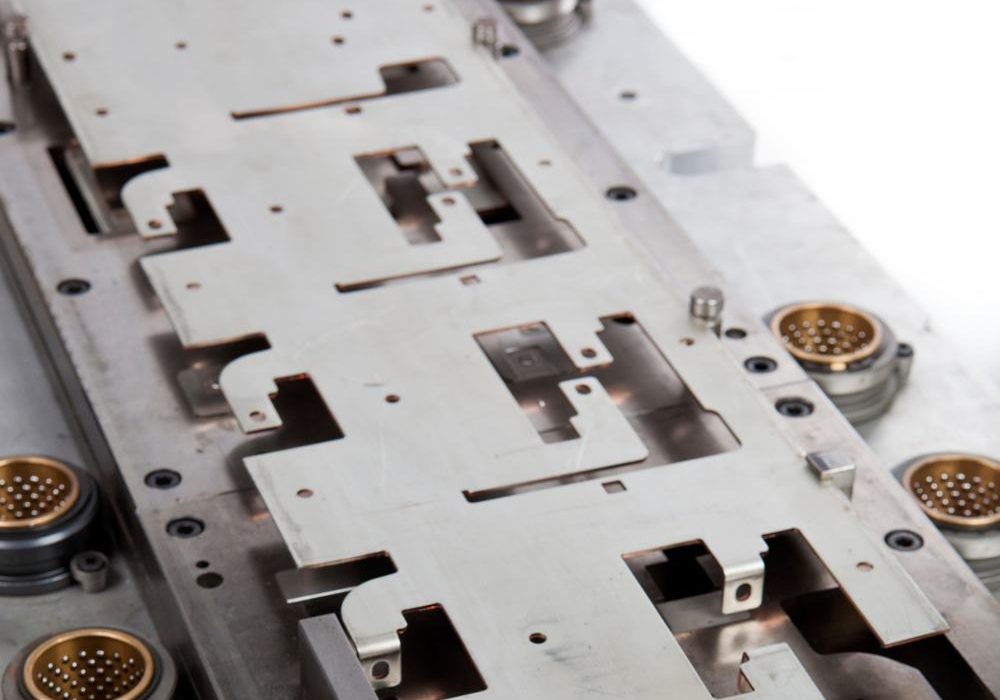
Advanced Feeding System Molds
Our selection includes Hot Runner Injection Molds for efficient material use and cycle times, Cold Runner Injection Molds for versatility in applications, and Insulated Runner Molds designed to reduce thermal loss. Each system is chosen to optimize the molding process based on your specific requirements.
Versatile Cavity Options
Whether you need a Single Cavity Injection Mold for specialized parts, a Multi Cavity Injection Mold for high-volume production, or a Family Injection Mold to produce different parts simultaneously, SONFUAT has the capability to design molds that precisely fit your production needs.
Innovative Mold Plate Designs and Unscrewing Molds
We provide Two Plate Injection Molds and Three Plate Injection Molds for straightforward or complex part ejection, along with Stack Injection Molds for high output efficiency. For components requiring threaded holes, our Unscrewing Injection Molds utilize advanced drive systems, including rack and pinion, electric motors, and hydraulic motors, to automate the process and ensure accuracy.
What Makes Us Stand Out?
Professional Team
Precision & Accuracy
Multi Materials
Industries That Use Production Molds
Automotive
Aerospace
Medical
Electronic
Applications Of Production Mold Making
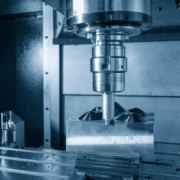
Benefits Of Using Production Mold Making
- High Efficiency and Productivity: Production molds streamline the manufacturing process, allowing for the mass production of parts with consistent quality. This efficiency significantly increases productivity and meets high-volume demands promptly.
- Cost-Effectiveness: Though the initial investment in production mold making might be significant, the cost per part is considerably reduced in high-volume production runs. This cost efficiency becomes more pronounced over time, making it an economically viable option for mass production.
- Superior Quality and Consistency: Production molds are engineered to exact specifications, ensuring that each part produced is of uniform quality and meets strict standards. This consistency is crucial for maintaining product integrity and customer satisfaction.
- Versatility in Materials and Design: Modern mold making technologies allow for the use of a wide range of materials and intricate designs. This versatility enables manufacturers to innovate and produce complex parts that meet the evolving needs of various industries.
Reduced Waste: Production molds are designed to minimize material waste, making the manufacturing process more sustainable. Efficient use of materials not only reduces costs but also aligns with environmental sustainability goals.
Faster Time-to-Market: By facilitating rapid production of parts, production molds can significantly shorten the time it takes to bring a product from concept to market. This speed is a competitive advantage in fast-paced industries.
Longevity and Durability: High-quality production molds are built to last, capable of producing millions of parts over their lifespan. This durability ensures a long-term return on investment, with minimal downtime for maintenance or replacement.
FAQs
Mold making is needed for several reasons:
- Mass Production: It enables the manufacturing of large quantities of parts or products efficiently, meeting high demand in sectors like automotive, consumer goods, healthcare, and more.
- Consistency and Quality: Molds ensure that each product manufactured is identical to the last, maintaining high quality and uniformity across production runs, which is crucial for consumer satisfaction and regulatory compliance.
- Cost-Effectiveness: Though initial mold design and creation may require a significant investment, the cost per unit produced is significantly lower, especially in high-volume production. This makes mold making a cost-effective solution for mass production.
- Material and Design Versatility: Modern mold making techniques allow for the use of a wide range of materials and can accommodate complex designs that would be difficult or impossible to achieve through traditional manufacturing methods.
- Speed: Mold making can significantly reduce production time, allowing for quicker turnaround from design to finished product. This rapid production capability is essential for staying competitive in fast-moving markets.
- Sustainability: By optimizing material use and reducing waste, mold making contributes to more sustainable manufacturing processes. Precise molds minimize excess material, contributing to environmental conservation efforts.
In summary, mold making is a critical component of the manufacturing industry, providing the means to produce high-quality, uniform products at scale, efficiently and cost-effectively, while also offering the flexibility to innovate and meet the dynamic needs of the market.
For plastic injection mold making, materials are selected based on their ability to withstand high pressures, temperatures, and corrosive plastics during the injection molding process. The most commonly used materials for this purpose include:
Steel:
- Tool Steel: High durability and able to endure the wear and tear of high-volume production cycles, making it ideal for long-term use.
- Stainless Steel: Chosen for its corrosion resistance, particularly important for molds used with corrosive plastics or for medical and food-grade products that require high levels of sanitation.
Aluminum:
- Used for lower-volume production or prototype molds due to its excellent thermal conductivity and lighter weight, which allow for faster cooling times and shorter cycle times. Aluminum molds are more cost-effective but less durable than steel molds.
Pre-hardened Steel:
- Offers a balance between wear resistance and machinability without the need for additional heat treatment, making it a quicker option for mold production.
Hardened Steel:
- Undergoes heat treatment to increase its hardness and durability, suitable for high-volume production molds where longevity and resistance to wear are crucial.
Beryllium Copper:
- Often used in areas of the mold that require fast heat removal due to its excellent thermal conductivity. It’s particularly useful in cooling channels to minimize cycle times.
P-20 Steel:
- A pre-hardened tool steel commonly used for injection mold making. It provides a good balance of cost, machinability, and durability, making it suitable for many applications.
H13 Steel:
- Known for its high toughness and hardness, H13 steel is used in molds that require resistance to thermal fatigue, such as those in high-temperature applications.
Each material choice for plastic injection molds balances the mold’s cost, performance, and longevity, influenced by the specific requirements of the production run, including the type of plastic material being molded, the complexity of the part design, and the expected production volume.
Yes, molds can be designed and manufactured in virtually any shape, depending on the complexity of the part being produced and the capabilities of the mold-making process. The versatility in mold design allows for the creation of parts ranging from simple, straightforward shapes to highly complex geometries with intricate details. This flexibility is one of the key advantages of using molds in manufacturing processes such as injection molding, die casting, and blow molding.
However, there are a few considerations to keep in mind when designing molds for complex shapes:
Draft Angles: To facilitate the easy release of the part from the mold, draft angles must be incorporated into the design, especially for parts with deep cavities or complex geometries.
Undercuts: Features that prevent the part from being directly ejected from the mold (known as undercuts) require special mechanisms, such as side-actions or lifters, making the mold design and manufacturing process more complex and potentially more costly.
Tolerances and Precision: Highly intricate shapes may require tight tolerances and high precision in mold manufacturing to ensure the final part meets specifications.
Material Flow and Cooling: The mold design must ensure uniform material flow and cooling to prevent defects, especially in complex shapes where uneven cooling can cause warping or sink marks.
Tooling and Machining: The complexity of the shape may necessitate advanced tooling and machining techniques, such as high-speed CNC machining, EDM (Electrical Discharge Machining), or 3D printing of mold components.
While molds can be made in any shape, the complexity of the design can impact the cost, production time, and the required technologies or techniques for mold manufacturing. Advanced mold design software and simulation tools are often used to optimize mold designs, ensuring manufacturability and addressing potential issues before the mold is made.
The lifespan of a production mold, often referred to as its “age,” can vary significantly depending on several factors including the material used to make the mold, the complexity of the mold design, the type of plastic being molded, the conditions under which the mold operates, and how well the mold is maintained. Here’s a general overview:
Mold Material:
- Steel Molds: High-quality steel molds, especially those made from hardened tool steels, can last for up to 1 million cycles or more under optimal conditions. They are preferred for high-volume production due to their durability.
- Aluminum Molds: Typically used for lower volume production or prototypes, aluminum molds may last for 100,000 to 500,000 cycles. Aluminum wears out faster than steel but offers quicker heat dissipation and shorter cycle times.
Mold Maintenance:
- Regular maintenance, including cleaning, lubrication, and inspection, can significantly extend a mold’s lifespan. Neglecting maintenance can lead to premature wear and damage.
Production Conditions:
- The injection molding process’s physical conditions, such as pressure, temperature, and the corrosiveness of materials used, also affect mold longevity. Molds used under harsh conditions will generally have a shorter lifespan.
Mold Design and Complexity:
- Simple molds with fewer moving parts and less intricate designs tend to last longer than complex molds with many moving parts or fine details, which may require more frequent repairs or adjustments.
Material Being Molded:
- The type of plastic material being molded can also impact mold life. Materials that are abrasive or corrosive may wear down mold components more quickly than less aggressive materials.
On average, a well-designed, well-maintained steel mold for high-volume production might be expected to last for several hundred thousand to over a million cycles. However, it’s crucial to consult with the mold manufacturer about the expected lifespan of a specific mold based on its design, intended use, and maintenance schedule to get a more accurate estimate.
Whether to use a completely automated mold depends on various factors related to your production needs, the complexity of the parts being manufactured, volume requirements, and cost considerations. Here are some aspects to consider when deciding if a fully automated mold is right for your operation:
Advantages of Fully Automated Molds:
Increased Production Efficiency: Automated molds can operate around the clock without human intervention, significantly increasing production capacity and efficiency.
Consistency and Quality: Automation reduces the variability associated with manual operations, ensuring consistent part quality and reducing the rate of defects.
Reduced Labor Costs: By minimizing the need for manual labor, automated molds can lead to substantial cost savings, especially in high-volume production scenarios.
Faster Cycle Times: Automated systems can optimize cycle times, making the production process faster and more efficient.
Enhanced Safety: Automation reduces the need for direct human interaction with the machinery, decreasing the risk of workplace injuries.
Considerations and Potential Drawbacks:
Initial Investment: The upfront cost of fully automated molds and the associated automation equipment can be significantly higher than that of manual or semi-automated systems.
Complexity and Maintenance: Automated systems can be complex and may require specialized maintenance and repair skills, potentially increasing downtime if issues arise.
Flexibility: While ideal for high-volume production of a single part or family of parts, fully automated molds might lack the flexibility needed for short runs or frequent product changes.
Technical Expertise: Implementing and optimizing automated molding processes requires a higher level of technical expertise, both in terms of equipment operation and maintenance.
Decision Factors:
- Volume: High production volumes typically justify the investment in automation due to the efficiencies and cost savings over time.
- Part Complexity: Simple parts with few variations are more suited to automation. Complex parts requiring frequent human intervention might not benefit as much from full automation.
- Cost vs. Benefit Analysis: Consider the long-term savings in labor and increased production capacity against the initial investment and ongoing maintenance costs.
- Future Needs: If your production needs are expected to change frequently, the flexibility of less automated systems might be advantageous.
Ultimately, whether to use a completely automated mold should be based on a thorough analysis of your specific production requirements, financial considerations, and long-term business goals. Consulting with a mold design and manufacturing expert can provide valuable insights tailored to your situation.
Where Craft Meets Engineering
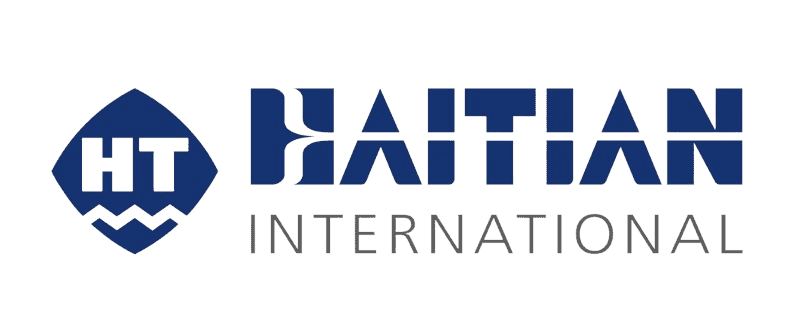
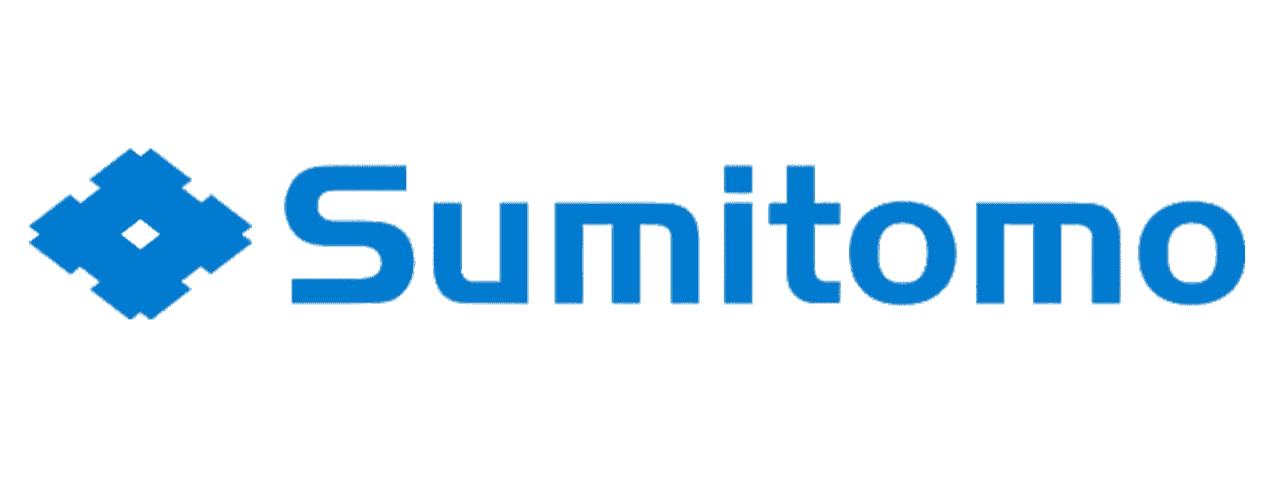
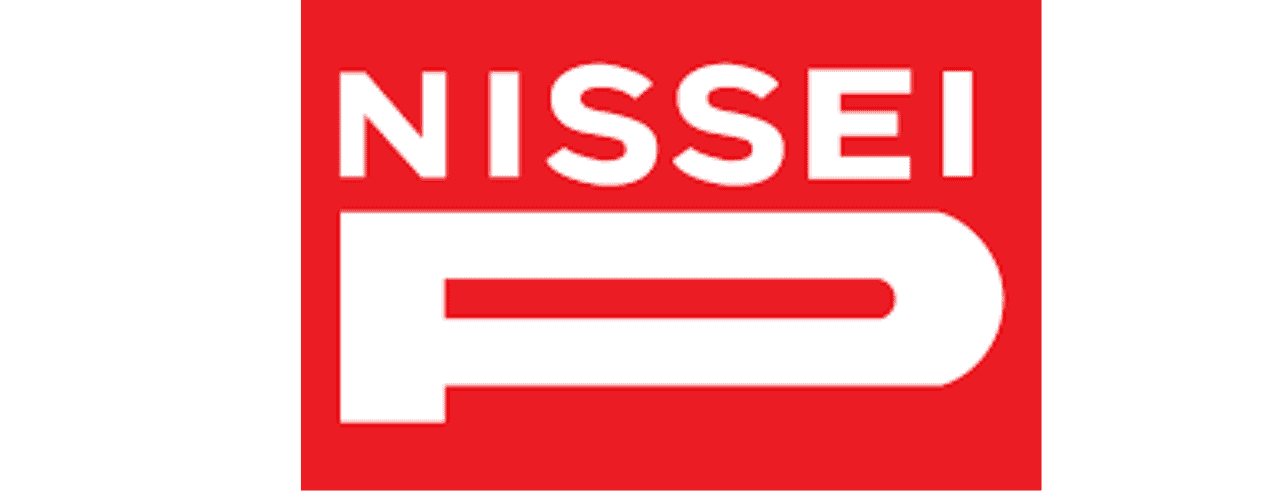
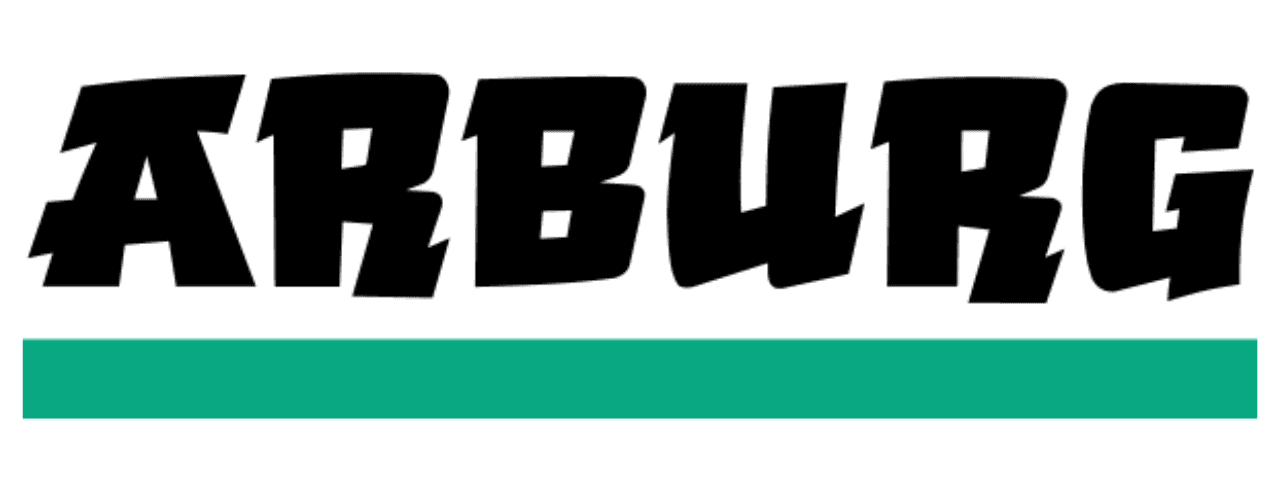